★ 壓塊原理
壓塊工序主要操控生球以下幾項目標:落下強度、濕球水分、粒度合格率。壓塊的強度與限制壓力、質料的粒度及粒度構成、粘結劑參加量、混料均勻程度,限制準則、壓塊的形狀等多種要素有關。生球塊水分和生球塊落下強度比照可知,生球塊水分和落下強度有必定聯絡:水分大時,生球塊落下強度有所上升;但生球水分過大,盡管塑性增強,且落下強度進步,但不利于枯燥及預熱等,下降生球塊的爆裂溫度。實踐證明,生球塊水分過大,必然延伸枯燥時刻。濕球塊枯燥時,因為球表里濕度差大致使不均勻縮短嚴峻,而使球塊發作裂紋,枯燥發作的裂紋可致使焙燒后球團強度下降67%~80%。此外,假如生球水分過大,枯燥時刻缺乏,當蒸騰面移向內部后,因為內部水分的蒸騰而構成的過剩蒸氣壓,使生球塊發作爆裂發作粉末,下降成品率。
生球塊的粒度在很大程度上決議了壓塊機的出產率和生球落下強度。粒度小,出產率高;粒度大,壓塊時刻長,出產率低,落下強度就越低。但粒度太小,抗壓強度就變小,然后影響了枯燥時的透氣性。因而,合理的生球粒度既是進步生球產值的需求,也是進步生球落下強度的需求。
★ 轉底爐復原鐵精礦原理
轉底爐復原鐵精礦主要是經過以下反響來完成的。
2Fe3O4+C=6FeO+CO2 式(3.1)
FeO+C=Fe+CO 式(3.2)
2Fe3O4+CO=3FeO+ CO2 式(3.3)
FeO+CO=Fe+CO2 式(3.4)
CO2+C=2CO 式(3.5)
反響式(3.1)、式(3.2)為直接復原反響,該反響為強吸熱反響,增加復原溫度有利于直接復原反響的加速。當溫度增加后,復原劑碳的反響活性進步,CO2反響率進步,增加溫度有利于進步產品的金屬化率,增加復原溫度或延伸復原時刻皆有利于鐵氧化物復原、鐵粉顆粒燒結。在粗復原過程中,也許發作固體碳氣化,鐵氧化物被直接復原,式(3.3)、式(3.4)為直接復原反響。CO2氣體與碳效果出產CO氣體。
轉底爐復原鐵精礦球團的基本原理(如圖3.1所示)是將焚燒著的火焰高溫經爐壁經過輻射傳給球團料層外表,使含碳球團中的鐵礦粉在高溫下被其間的碳和蒸發分復原。這種技術的特點是:
1) 選用這種輻射傳熱,避免了“輻射”和“傳質”之間的對立。
2) 技術簡略,對冶金資本適應性強,建造費用低。
3) 燃料利用率高,無碳氫化合物排放。在該技術中,煤粉帶入的蒸發分將充沛焚燒,不存在碳氫化合物的排放而污染環境疑問,這可大幅度下降環保開支。另一方面,煤粉帶入的碳也可大部分被轉化為CO,燃料利用率高。
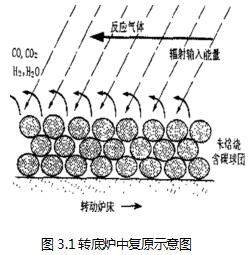
可是,火焰的高溫熱量要靠輻射傳熱,只能到達料層外表,有些熱量經過料層的空地輻射也只能到達外表(l~2)層的當地。這使得Fastmet法在爐底上只能鋪(2~3)層球團,厚度為(20~30)mm擺布。既使球團在爐內復原速度快,停留時刻也只要20min擺布??墒巧a率比通常燒結或球團技術差不多低了一個數量級,與燒結-高爐法平等規劃比較,需建的轉底爐的“復原面積”比燒結機的“燒結面積”大十倍以上。
生球經過給料槽堆放在轉底爐上(如圖3.2),厚度為20mm,完結反轉一圈之前經過水冷螺旋從爐中卸出。爐子的裝料段和缺料段是經過兩塊擋板與反響段離隔。爐膛和球旋轉方向與焚燒和反響生成的氣流方向相反。爐子溫度是借助于經過內外墻的燃料燒嘴來進行操控的,爐子內有不一樣的兩個焚燒區,一個是氧化性氛圍的球團預熱區,另一個是復原性氛圍下的復原區。球團在一次滾動中經過上述兩個區,金屬化率可高達92%,滾動一星期所需時刻取決于反響才能和氧化物的復原性,規模為(20~40)min。
為了確保疾速加熱,爐床上球團的厚度為3層,在球團料到達反響溫度后,碳和氧化鐵的嚴密觸摸使復原反響可以在全部球團截面上均勻而疾速的進行。
發生的CO不只用于氧化物的復原及焚燒進程,因為在球團料床上構成CO的薄層,還能對新復原的鐵起維護效果,然后避免了球團的再氧化。
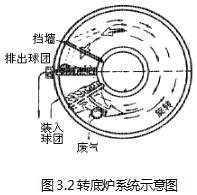
金屬化球團在約900℃下出爐,假如金屬球團在熱態下裝進熔煉爐,與冷態裝料比較,每噸球團料可節省電(200~250)KWh。因為轉底爐復原時間短,球團在爐床上停留時間為(20~40)min,在這段時間內90%~95%的氧化物轉變成金屬鐵。轉底爐能完成疾速復原,是因為復原溫度(1300~1400)℃比別的工藝高300℃擺布,并且球團中的碳與氧化物直接觸摸,反響的動力學條件較好。